A guide to cardboard boxes
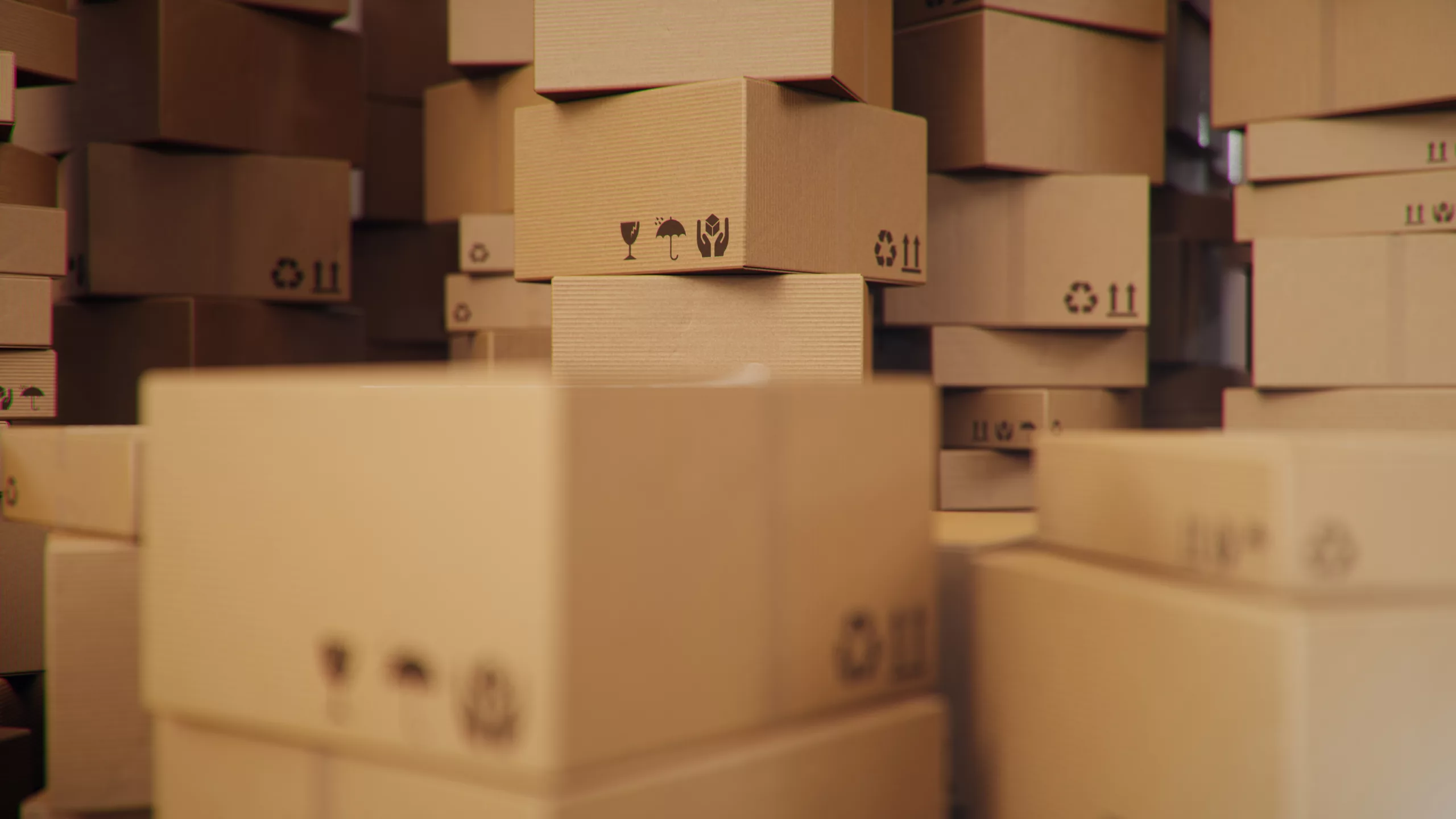
Corrugated cardboard is one of the most used materials in the world.
It’s said that ‘more than 12.5 million tonnes of paper and cardboard are used every year in the UK’. Considering the continued growth of online retail, it’s safe to assume that the popularity of cardboard boxes is here to stay!
Cardboard boxes are a much-loved packaging material used by everyone, from large multibillion pound ecommerce retailers to small Etsy shops! It’s the first product people think about when they say ‘packaging’. They have great versatility, to protect and ship your products and they can be recycled!
This guide will cover everything you need to know about cardboard boxes, to learn what will best suit you and your business. But first, a history lesson…
- 1.
- 2.
- 3.
- 4.
- 5.
- 6.
- 7.
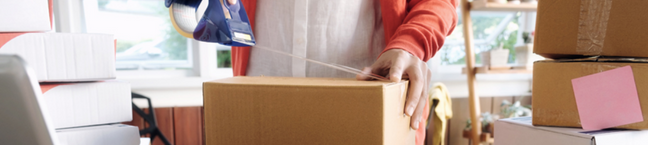
The history of cardboard boxes
Corrugated paper was first invented in the 19th century as a means to reinforce top hats! The first pleated paper was patented in England in 1856 by Edward G. Healy and Edward E Allen.
Almost two decades later, people started to use corrugated paper as a protective packaging material. Initially, it was used to wrap glass bottles and kerosene lamp chimneys. Corrugated cardboard as we now know it, came about in 1874 when an American, Oliver Long, introduced two sheets (or liners) to the pleated paper and make it stronger.
Flash forwards another 20 years to 1894 and the first corrugated cardboard boxes were produced by Henry Norris and Robert Thompson. They proved cheaper, lighter and easier to store than the wooden boxes being used for shipping at the time – and the packaging industry has never looked back!
To learn more about cardboard boxes, download our full guide today!
So, what do you need to know about corrugated cardboard boxes if you want to use them as your main packaging material? Well the size is a good place to start, as well as the specification of the type of cardboard you need…
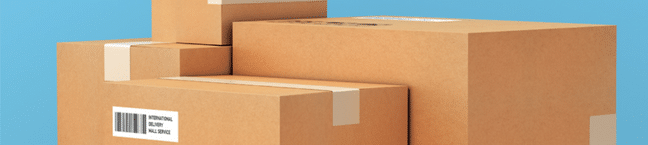
How to measure a cardboard box
The dimensions of a cardboard box always refer to the internal measurements (the usable space that your products will go in), not external; this is because different grading and fluting, it can alter the thickness of the cardboard itself. Cardboard box dimensions are usually expressed as: Length (L) x Width (W) x Height (H).
- Length = the longest opening dimension
- Width = the shorted opening dimension
- Height = the dimension from the top of the opening to the base of the box (sometimes referred to as depth).
We always recommend measuring cardboard boxes in millimetres. For example: 600mm x 300mm x 250mm.
The cardboard boxes you choose should accommodate the range of product you stock – from the smallest item to the largest – as well as any protective packaging (e.g., bubble wrap or paper cushioning) you’ll need for shipping.
Ensuring you get the size of your cardboard boxes right is important, due to the effect across your supply chain; from minimum order quantities, through to storage and customer experience.
Quick tip – If your cardboard box is too big, it can lead to product damage through in-pack movement and excess packaging waste. Too small might have to reduce how much protective materials are used, meaning increase product damages.
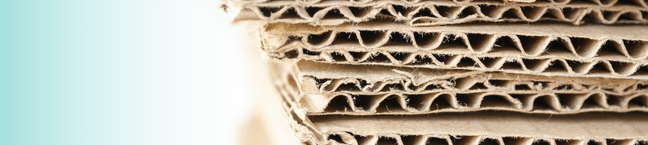
Understanding the types of corrugated cardboard and cardboard box specifications
Most cardboard boxes are made from corrugated cardboard. This type of cardboard is made from a fluted or waved piece of paper sandwiched between two flat pieces of paper.
There are three main types of corrugated cardboard you’ll come across when it comes to boxes:
- Single wall – one layer of fluted board is sandwiched between two sheets of liner board. This would make a single wall cardboard box.
- Double wall – two layers of fluting that are glued to three layers of liner board. This would make a double wall cardboard box, which is stronger than using single wall alone.
- Triple wall – three layers of fluting are laminated with four liner boards. This would make a triple or tri-wall box – the most heavy-weight and durable of all boxes.
Fluting profiles
Fluting is the wavy or fluted piece of paper inside corrugated cardboard that helps to strengthen the boxes. It’s what creates the stripey grain like texture you would see when looking at a piece of cardboard.
It can vary in width and size and is often referred to by letter e.g., “B flute”. Single wall boxes will only have one type of fluting, but double and triple wall boxes may use multiple fluting profiles.
Board grades
The board grade refers to the weight, quality and type of material used to make the cardboard. Depending on the intended use of a box, the board weight will range from 90gsm to 300gsm.
The heavier the weight of the paper, the stronger the box will be. It’s worth noting that the GSM description of the board may relate to the performance of the board, and not the actual weight. In other words, it has the properties of a heavier material.
As well as the weight of the paper, you may also hear the words “kraft” or “test”. These terms relate to if the paper used in manufacturing is virgin material (kraft) or recycled material (test). Some boxes may combine both kraft and test cardboard.
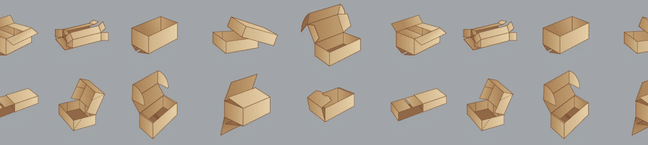
Styles of cardboard boxes
You can choose from a range of internationally standardised boxes. All of these are dictated by FEFCO – the European Federation of Corrugated Board Manufacturers.
There are nine different categories of cardboard boxes, which are then broken down into different styles. The most common box style is 0201, which is a slotted type of box. Another common box style is 0427, which is a folder style box, sometimes called a pizza style box.
What is the advantage of each type of cardboard box?
- 0200 – An open top box with flaps meeting at the base, which need to be sealed. Often linked with the 0422 lid and used for storage.
- 0201– The most common corrugated case. Outer flaps meet at the top and bottom, requires sealing. It will not require any tooling unless it needs modification for specialist erecting machines. This is the most economical way to pack most products. The side seam is usually glued but can be stitched. Stacks well.
- 0202 – Similar to 0201 but with the outer flaps overlapping by a specified amount. Ideal for cases where extra strength and security are needed. Excellent for use with polypropylene strapping as the method of securing.
- 0203 – Similar to the 0201 but the flaps fully cover the base and top. This gives added strength to the case especially if taped in certain ways.
- 0301 – Tray and lid. Used for shallow products and an economical way to purchase this format as it can be made without tooling. However, the corners of the lid and tray would need to be sealed. A neater solution would be the 0422, particularly if the volume required is significant.
- 0310 – A combination pack of 0501 sleeve with 0452 top and bottom caps (not featured). Generally used for pallet packs or with automated packing systems. Requires stitching or gluing of the caps.
- 0713 – Ready-glued cases consist of basically one piece, are shipped flat and ready to use by simple setting up.
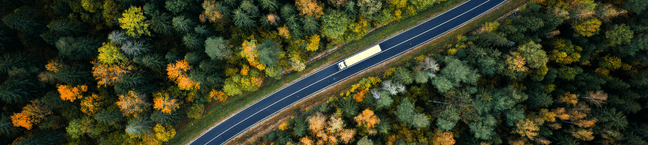
Cardboard boxes and recycling
We’re often asked are cardboard boxes recyclable? The short answer is yes!
Cardboard boxes are widely recycled and frequently collected at kerbside by local authorities. It’s worth noting that to make it as easy as possible to recycle any cardboard material that you check the following:
- Plastic tape, document wallets and labels are removed from boxes so they don’t contaminate the material or hinder the recycling process
- Contaminated cardboard is not put into recycling collections – for example, pizza boxes covered in crease or food might not be recyclable
For information about how to recycle other packaging materials, read our handy guide.
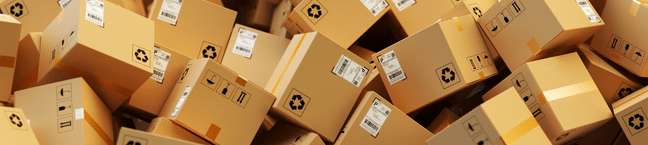
Cardboard boxes quick tips
- Cardboard box dimensions are usually expressed as: Length (L) x Width (W) x Height (H).
- Always measure the inside of the box (the usable space), not the outside
- Don’t forget to account for the size of protective materials you use when considering box sizes
- The common types of cardboard boxes are single wall, double wall, and triple wall.
- Contaminated cardboard is not put into recycling collections – for example, pizza boxes covered in crease or food might not be recyclable
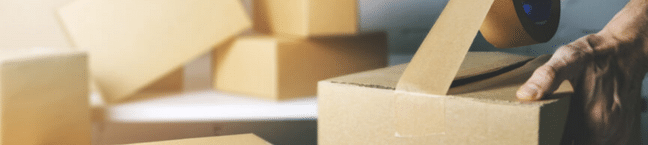
Cardboard box glossary
- Single wall – one layer of fluted board is sandwiched between two sheets of liner board. This would make a single wall cardboard box.
- Double wall – two layers of fluting that are glued to three layers of liner board. This would make a double wall cardboard box, which is stronger than using single wall alone.
- Triple wall – three layers of fluting are laminated with four liner boards. This would make a triple or tri-wall box – the most heavy-weight and durable of all boxes.
- Fluting – the wavy or fluted piece of paper inside corrugated cardboard that helps to strengthen the boxes.
- Board grade – the weight, quality and type of material used to make the cardboard.
- FEFCO – the European Federation of Corrugated Board Manufacturers – they standardize box styles.
- MOQ – Minimum Order Quantities – If you chose to get custom boxes created, you may face MOQ meaning you have to order a certain amount of stock. This often depends on the size of the box – the smaller it is, the higher the MOQ.
- 0201 – The most common corrugated box style. Outer flaps meet at the top and bottom, and requires sealing.
Still not sure what cardboard box you need? Contact us today for expert help and advice.