3 quick-install packaging automation systems for ecommerce
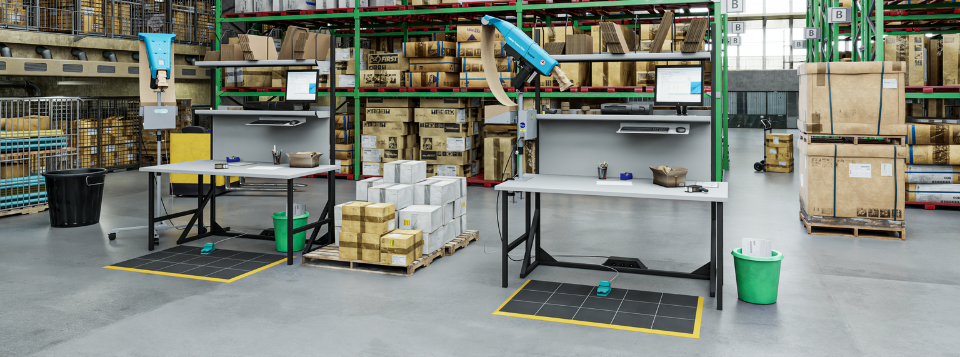
The peak season for online shopping is fast approaching, and retailers are preparing to manage increased orders and demands..
If you are an internet retailer, you will be no stranger to the challenges that peak seasons bring.
During busy times like holidays or promotions, being able to process orders quickly is crucial for your business’s success. One of the critical components of managing this surge is your packaging process. This is where quick-install packaging machinery comes into play.
One way to streamline the packing process and boost efficiency is by implementing packaging automation. Fully integrated packaging automation takes a lot of time and planning. What we are focusing on in this article are quick and easy semi-automatic installations that are plug and play – simply set up where needed and remove some of the manual interventions needed when packing your products. The machines we will discuss will help make your operation more efficient and getting your shipments out of the door quickly during the busiest quarter of the year.
Quick-install packaging machinery provides an ideal solution for businesses looking to streamline their operations without the downtime associated with traditional fully integrated packaging automation and systems.
In this blog, we will focus on three key types of packaging automation that are easy to install, along with the benefits of each. We also provide a checklist to help you prepare your business for automation.
- 1.
- 2.
- 3.
- 4.
- 5.
- 6.
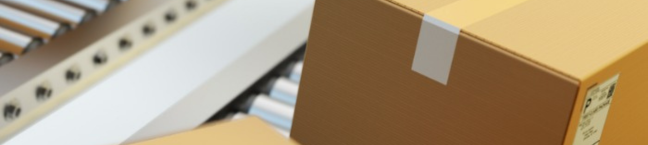
Why choose packaging automation for e-commerce?
Automating your packaging processes can significantly enhance your packing operations.
One of the primary benefits of automated packaging systems is the cost savings and efficiency improvements they bring. Automation reduces labour costs and minimises human errors. Machines handle high order volumes, ensuring quick and accurate packaging, even during peak periods.
Automated packaging systems streamline order processing and packaging applications, enabling you to meet tight delivery deadlines. Improved turnaround times exceed customer expectations, resulting in positive reviews and repeat business.

What is the difference between semi-automatic and fully automatic systems?
Packaging automation is available with semi-automatic or fully automatic capabilities, which determines how much manual intervention is required by operators.
Semi-automatic systems involve a part-manual and part-automated process. For example, a box may be assembled and packed by the operator, but the machine will seal the pack.
A fully automatic packaging system will complete the task from start to finish. For example, assembling a box, adding void fill then sealing.
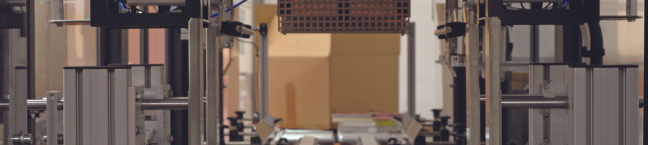
1. Box sealing
There are a few options available to ramp up the automatic sealing of your parcels. Manually applying tape to your boxes can take up to 60% of your overall packing time when using traditional shipper cartons.
The entry level quick-install step is to switch to a programmable electronic tape dispenser and water-activated tape. These produce ready-cut lengths of tape at the touch of a button, removing the need to apply and tear the tape with a manual handheld dispenser. Electronic Water activated tape dispensers are available either in a static workbench format, like the BP555 or, an on-the-go handheld device that can be used throughout the warehouse, like the Grip Taper.
It’s worth noting that water-activated tape forms a stronger bond with corrugated material too. Therefore, the finished box is tamper-evident and easily recycled!
Some benefits of automated case sealers are:
Speed: Speeds up the sealing process by up to 60%.
Material savings: Dispenses the exact amount needed each time, reducing cost and material waste.
Versatility: Programmable so it can be configured to your in-house box range.
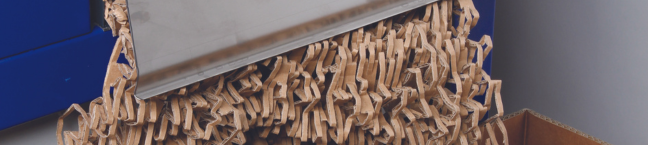
2. Void fill systems
Automated void fill systems use air pillows or paper to protect products during shipping by filling empty spaces in packaging. These are perfect for businesses that ship delicate or oddly shaped items and want to make sure they arrive safely.
Void fill systems for airbags are available with a small footprint, so they can be easily installed on a pack bench to dispense void fill materials at the touch of a button – or foot pedal. Systems like the Mini Pak’r® or Pro Pak’R® offer recycled content airbag film too – so it’s a win for you and the environment.
Paper systems can be desk mounted or, height adjusted to stand behind the pack bench, this means it can dispense void fill materials directly into the box. A good example of this in action are the Ranpak FillPak® systems.
Some benefits of automated void fill systems are:
Damage Reduction: Minimises product movement within the box, reducing the risk of damage.
Speed: Quickly fills voids, keeping the packaging process fast and efficient.
Material Savings: Optimises the amount of filler used, reducing waste and costs.
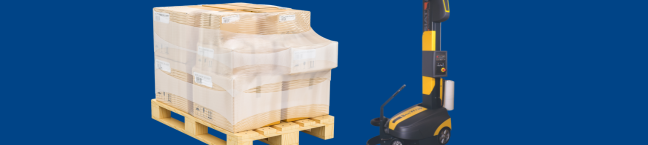
3. Pallet wrapper machines
Semi-automatic stretch wrap machines wrap products or pallets in stretch film to secure them for shipping. They are perfect for retailers who ship large amounts of goods on pallets to distribution centres or even direct to customers.
The system wraps the pallet automatically, leaving the operator free to prepare the next pallet for wrapping.
The benefits of an automated stretch wrapper are:
Stability: Provides additional stability to pallets, reducing the risk of products shifting or falling during transit.
Protection: Offers a layer of protection against dust, dirt, and moisture.
Efficiency: Reduces the amount of stretch film used, limiting material costs and waste.
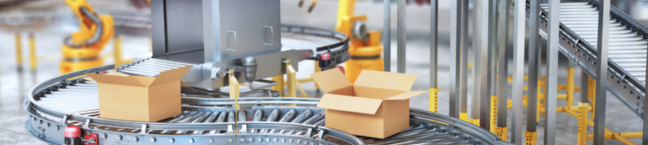
How to select and install the best packaging automation for your business
To maximise the benefits of quick-install packaging machinery, we have pulled together a short checklist to ensure installation success.
1. Assess your current packaging process:
Identify bottlenecks and areas where automation can provide the most benefits. Consider factors such as packaging volume, product types, and available space.
2. Choose the right machinery:
Select machinery that fits your specific needs. Consider the types of products you package, the volume of orders, and the layout of your packaging area.
3. Plan the installation:
For quick-install machinery, planning is minimal. However, if you want to install more integrated systems, you will need to develop a detailed plan. This should include timelines, responsibilities, and contingency plans to address potential issues.
4. Train your staff:
Make sure your team knows how to operate the new machinery. This training should cover setup, operation, maintenance, and troubleshooting.
5. Test and optimise:
After installation, run tests to ensure the machinery is functioning correctly. Monitor performance and make any necessary adjustments to optimise efficiency.
Quick-install packaging machinery offers internet retailers a powerful tool to prepare for peak seasons. These machines can enhance your packaging operations by increasing efficiency and quality. They can help you meet higher demand without compromising customer satisfaction. The machines are capable of quickly expanding and improving your packaging processes.
At Macfarlane Packaging, we can help you to identify and install the right packaging automation to improve efficiency. Contact us today!